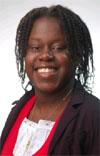
Mechanical Engineering 2009
Area of Doctoral Study: Mechanical Engineering
Research Advisor: Timmie Topoleski
Undergraduate Institute: University of Connecticut
Current Position: Assistant Professor, Volgenau School of Engineering, George Mason University
Description of Research
There are over 500,000 total joint replacements (TJR) performed in this country every year and TJR remains the most successful treatment for arthritis [1]. Total joint replacement (TJR) is one of the most common surgical treatments for patients with severely damaged joint cartilage due to conditions such as osteoarthritis (OA), rheumatoid arthritis and post-traumatic arthritis. TJR is designed to restore pain free joint movements in the diseased joint. Currently, the most commonly used materials for artificial joints are cobalt-chrome or titanium alloys, articulating against ultra-high molecular weight polyethylene (UHMWPE) [2]. However, the production of excessive amounts of polyethylene wear debris had been linked to osteolysis (i.e. bone loss), which may result in further component loosening. To eliminate wear caused from polyethylene designs, the use of metal-on-metal implants has been renewed for total hip replacements and the various aspects of metal-on-metal bearings have been studied.
Improvements in wear rates have occurred through the of the use of alternative bearing materials such as wear resistant ceramics in combination with ultra-high molecular weight polyethylene, alloys and other ceramics. Our new micro-textured carbide surface layers created by a microwave plasma assisted chemical vapor deposition reaction (MPCVD) produced a functionally graded material composed of a ceramic carbide surface layer, a carbon diffused subsurface layer, and the original alloy matrix. This newly developed carbide coated cobalt-chrome-molydenum (CoCrMo) showed potential for improving the wear performance of CoCrMo alloy. The purpose of this study is to determine: does the use of carbide-coated CoCrMo alloy with an artificial fluid lubricant improves the wear characteristics compared to non-coated CoCrMo. Bovine calf serum at varying concentrations will be used as for the artificial lubricant. In particular, this research will focus on the tribological wear and mechanical properties such as elastic modulus and hardness, as a function of lubricant composition and surface roughness of the micro-textured carbide for seven different wear couple systems.
- Arthritis Foundation, http://www.arthritis.org/
2. McKellop H, et al. Wear characteristics of UHMW polyethylene: a method for accurately measuring extremely low wear rates. J Biomed Mater Res 1978;12(6):895-927.